L’efficienza produttiva cresce di pari passo con la capacità di innovare, la digitalizzazione e… la sostenibilità. E’ il punto di partenza del confronto con Wonderware che propone una serie di tecnologie abilitanti in grado di migliorare l’efficienza e di approdare ad uno scenario di coordinamento digitalizzato delle operation così da perfezionare i processi, gestire il workflow produttivo, ma allo stesso tempo ridurre anche gli scarti, l’inefficienza della macchine, il cosiddetto “rework” con una maggiore flessibilità. Ne parliamo con Massimiliano Braga, Consultant Leader di Wonderware.
In che modo Wonderware supporta le aziende nell’indirizzare sostenibilità ed efficienza operativa all’interno delle loro fabbriche?
La sostenibilità è un tema estremamente sentito da tutte le realtà produttive per tre motivazioni: una di tipo etico, normativo e di mercato. Oggi tra le prime cinque cause di maggiore emissione di CO2 ritroviamo il fattore energetico, i trasporti e il manufacturing tutti temi che sono coinvolti nella supply chain. Focalizzando l’attenzione sulla parte produttiva, ossia lo stabilimento, che è l’ambiente in cui Wonderware Italia ormai da quasi 30 anni opera quotidianamente sviluppando soluzioni di digitalizzazione, possiamo dire con certezza che innovazione, efficienza produttiva e digitalizzazione vanno di pari passo con la sostenibilità. Smart Factory non è solo sinonimo di innovazione tecnologica nel modo di produrre ma acquista un significato di fabbrica sostenibile. Industry 4.0 e 5.0 hanno ridotto significativamente gli ostacoli all’implementazione di soluzioni intelligenti. Sono diverse le tecnologie abilitanti che noi offriamo e uno strumento di efficientamento è il Mes (Manufacturing Execution System) che permette un coordinamento digitalizzato delle operation e ottimizza il processo, gestire il workflow produttivo riducendo gli scarti, l’inefficienza della macchine, ridurre il rework e dare flessibilità. Ma anche tutti gli altri strumenti che applichiamo presso i nostri clienti per dare visibilità in tempo reale alle grandezze che impattano le emissioni. Creando data platform di questo tipo rendiamo possibile ai nostri clienti di quantificare il risparmio di CO2, tonando sul mercato e offrendo il giusto prodotto che oggi il consumatore più attento richiede. Per citare un esempio: Vishay, cliente Wonderware, leader sul mercato internazionale di componenti elettronici. Siamo partiti da una situazione iniziale in cui il sito emetteva 7000 t di C02, è stata implementata una soluzione basata sulla nostra Data Platform e il cliente ad oggi ha già raggiunto una sostanziale riduzione di emissioni di gas ad effetto serra.
Come la manutenzione degli impianti può impattare positivamente sulla sostenibilità delle aziende?
L’aspetto manutentivo è un aspetto molto sensibile nelle realtà produttive perché ha un impatto diretto sulla produzione. Gli obiettivi della manutenzione non sono più solo il miglioramento continuo dell’affidabilità, della manutenibilità, dell’efficienza del “sistema”, della stabilità dei processi (assicurazione qualità), o la conservazione del patrimonio impiantistico piuttosto che l’ottimizzazione dei costi degli interventi stessi, bensì anche il concorso al miglioramento degli aspetti ambientali e della salute e sicurezza, in linea con quanto richiesto oggi dagli obiettivi per lo sviluppo sostenibile dell’Agenda 2030.
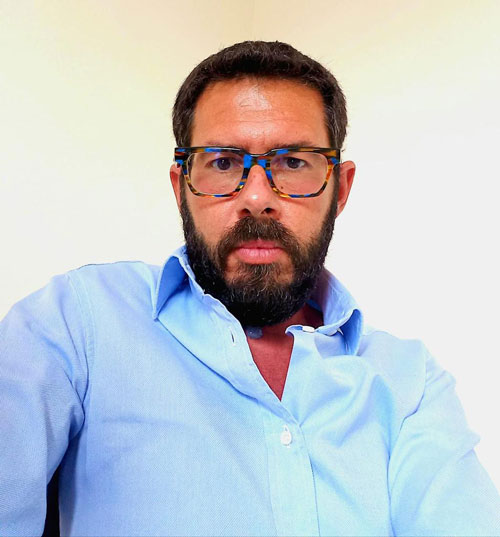
Se prima indicatori come Mtbf (Mean Time Between Failures), Mttr (Mean Time to Repair) e Oee davano indicazione prestazionale ed economica adesso acquisiscono un significato legato alla sostenibilità. Parliamo oggi di manutenzione preventiva o anche predittiva cambiando completamente l’approccio rispetto all’intervento di quando il guasto è già avvenuto. Spesso accade che al momento del guasto ciò che si sta lavorando diventi scarto o prodotto da rilavorare, ma soprattutto si crei una grossa inefficienza. Lo scarto non solo genera materiale da smaltire ma ha creato un consumo energetico della linea inutile con impatto sulla emissione di CO2. E a sua volta indirettamente si lega alle emissioni derivanti dalla catena di fornitura delle materie prime. Questo è un percorso attraverso il quale, come Wonderware, stiamo accompagnando i nostri clienti spostando l’attenzione verso la manutenzione preventiva basata su condizione e quindi controllabile attraverso una soluzione nel nostro portfolio. Basf, multinazionale nel settore chimico, ha iniziato questo percorso con noi su tematiche legate alla manutenzione che coinvolgono aspetti legati non solo alla sicurezza ambientale ma anche quella sociale delle persone coinvolte nella produzione.
Quali sono i suggerimenti che Wonderware si sente di dare a un’azienda che punta ad ottimizzare i proprio processi di Production planning?
Ottimizzare i processi di pianificazione e schedulazione sono elementi di grande impatto in termini di efficientamento delle risorse produttive, dei team di lavoro e anche di sostenibilità. Tutte le soluzioni che Wonderware propone clienti non hanno solo un aspetto tecnologico ma al tempo stesso un approccio consulenziale affrontando le tematiche su cui intervenire e sviscerando al meglio la consueta e frequente risposta del ‘lo abbiamo sempre fatto cosi’. La tecnologia ha un impatto sulle persone ed è per questo che coinvolgere il business nelle nostre soluzioni è un aspetto che teniamo sempre in considerazione. Una buona schedulazione nasce anche da una buona consapevolezza a saper reagire a situazioni inaspettate, che richiedono tempi di reazione rapidi. Questo è possibile avendo pieno controllo su processi tramite la capacità di monitorarli e misurarli con gli strumenti digitali corretti. Una soluzione di scheduling, deve essere interpretata come facente parte di un piano più ampio in cui vengono presi in considerazione altri aspetti organizzativi come la manutenzione ed il monitoring dell’avanzamento della produzione in tempo reale. Ovviamente i vantaggi di inserire uno strumento di schedulazione a capacità finita sono innumerevoli e rispondono alle sfide che ogni giorno chi schedula la produzione deve affrontare: saturazione delle linee, ottimizzazione dei tempi di attrezzaggio, riduzione dei Wip (work in progress), ottimizzazione delle sequenze produttive valutando i routing possibili, saturazione del personale tenendo conto di un numero finito di risorse con skill ben definiti. E soprattutto supportando le richieste del mercato di avere lead time sempre più brevi con dimensioni di ordini sempre più ridotte e frequenti.
Leggi tutti gli approfondimenti della Room Barometro Integrated supply chain 2023
© RIPRODUZIONE RISERVATA