Crescono le pressioni competitive sul mercato manifatturiero. I clienti si aspettano innovazione rapida, personalizzazione sartoriale dei prodotti e livelli di qualità elevati, mentre le aziende devono tenere sotto controllo costi, con tempi di consegna e cicli di vita del prodotto sempre più ridotti. In questo contesto, diventa cruciale ripensare i tradizionali modelli di gestione puntando su un’integrazione efficace tra sistemi Product Lifecycle Management (PLM), Enterprise Resource Planning (ERP) e Manufacturing Execution System (MES). L’obiettivo è sincronizzare i dati di progettazione con le operations di produzione, garantendo tracciabilità, efficienza e contenimento dei costi lungo l’intero ciclo di vita di ogni prodotto. Per operare in modo corretto è fondamentale considerare i principali fattori che spingono verso questa integrazione, le sfide da affrontare per raggiungere la migliore sinergia tra PLM, ERP e MES, e i benefici derivanti da un ambiente connesso, in cui la qualità dei dati di progettazione e di produzione diventa il vero motore dell’ottimizzazione operativa. Entriamo nei dettagli.
Produzione sotto stress
La richiesta di prodotti sempre più ricchi di funzionalità, personalizzabili e, al tempo stesso, capaci di mantenere standard qualitativi elevati, gli scambi globali e la velocità dell’innovazione tecnologica spingono a progettare e immettere in produzione un maggior numero di modelli, varianti e configurazioni, generando un notevole stress sui processi di sviluppo e fabbricazione. Non vale solo per l’ambito produttivo: anche logistica e supply chain devono reagire rapidamente alle fluttuazioni della domanda, mentre i reparti di assistenza e manutenzione si trovano a intervenire su prodotti via via più complessi. Questa situazione impone di rivedere in chiave digitale la gestione delle informazioni di prodotto, dal concept iniziale fino al supporto post-vendita, passando per la prototipazione, l’industrializzazione e la messa in opera. Alla base di tutto risiede la necessità di disporre di dati sempre aggiornati. Poiché gli stessi dati (distinte base, specifiche, configurazioni) devono essere consultati e modificati in più momenti e da vari reparti, per questo la creazione di un “digital thread” condiviso – in cui PLM, ERP e MES siano perfettamente allineati – è decisiva per ridurre gli errori, contenere i costi e velocizzare il time-to-market.
Una crescente complessità
La crescente complessità della produzione moderna porta con sé diverse criticità operative. In primo luogo, la tracciabilità di materiali e processi: filiere lunghe e internazionali, varianti di prodotto e reparti frammentati rendono più arduo tenere sotto controllo ogni fase. Se i sistemi informativi non comunicano in modo fluido, possono formarsi “isole” di dati che ostacolano l’identificazione tempestiva di difetti, colli di bottiglia o ritardi. In queste condizioni, le azioni correttive (come i richiami) risultano costose e tardive, perché non si dispone di una visione chiara di ciò che accade in officina. Un ulteriore fattore critico è la pressione sui costi: la concorrenza globale richiede di offrire prodotti di alta qualità a prezzi competitivi. Poiché fino al 70% del costo di un articolo si definisce già in fase di progettazione, eventuali errori o mancate collaborazioni tra reparti (ad esempio tra R&D, ingegneria di produzione e supply chain) rischiano di generare spese elevate a valle, difficili da compensare. Gli sprechi di materiali, gli interventi di correzione sul prodotto finito e i rallentamenti nei cicli di fabbricazione si traducono in inefficienze che incidono pesantemente sui margini. A complicare ulteriormente il quadro interviene la carenza di personale esperto e il turnover, fattori che rendono più complicato trasferire le competenze in maniera informale. Di conseguenza, la gestione e il riutilizzo della conoscenza richiedono una piattaforma centralizzata e affidabile, a cui tutti possano attingere. Un’integrazione evoluta dei sistemi enterprise permette di costruire una base condivisa di informazioni, utile per orientare le decisioni strategiche e aiutare i nuovi addetti a recuperare rapidamente il contesto di lavoro.
Integrare il PLM, valorizzare il potenziale dei sistemi di gestione
Tradizionalmente, la progettazione dei prodotti (con tutti i dati e specifiche) è sempre avvenuta nel PLM, per poi passare “a valle” le informazioni a ERP e MES con flussi spesso manuali o parzialmente disconnessi. Oggi, però, a causa dell’elevata complessità di design e della rapidità con cui si susseguono i cambiamenti, un approccio frammentato non è più sostenibile. Diventa cruciale integrare il PLM sin dalle prime fasi di innovazione e lungo l’intero percorso di preparazione della produzione, in particolare per due motivi. In primo luogo, la gestione avanzata delle configurazioni: i prodotti vengono proposti in più varianti e opzioni. Mantenere la coerenza tra la distinta base di ingegneria (EBOM, Engineering Bill Of Materials), la distinta base di fabbricazione (MBOM, Manufacturing Bill Of Materials) e le eventuali distinte ricambi (SBOM, Software Bill Of Materials) risulta complicato, se i sistemi lavorano in modo isolato. Far convivere tali distinte nello stesso ambiente, con aggiornamenti in tempo reale, garantisce che gli operatori ricevano sempre i dati più recenti, riducendo i passaggi ridondanti.

In secondo luogo, la possibilità di automatizzare i processi: se ERP e MES non sono strettamente integrati col PLM, ogni modifica progettuale deve essere reinserita a mano, moltiplicando il rischio di errori e incrementando i costi. Un flusso digitale continuo (digital thread) assicura che gli aggiornamenti alle distinte base o ai piani di produzione vengano recepiti automaticamente dai reparti competenti; al contempo, i feedback provenienti dal campo (come segnalazioni di non conformità o suggerimenti di miglioramento) vengono inviati “a monte”, influenzando positivamente le fasi future di progettazione.
In questo quadro, si rende necessario riequilibrare i confini tra i sistemi: all’ERP spetta la pianificazione della domanda, la gestione dei costi, l’approvvigionamento e la logistica; il PLM gestisce i dati di prodotto, la pianificazione del processo e il change management; il MES si occupa dell’esecuzione in fabbrica e monitora in tempo reale la produzione. Ciascun sistema possiede, dunque, un ambito ben definito, senza sovrapposizioni dannose che generino duplicazione dei dati o confusione, ma tutti i sistemi devono essere integrati e dialogare tra loro.
Il valore dei dati, la capacità di gestirli
La riuscita di questo approccio dipende in larga parte dalla qualità dei dati (in particolare dei dati master) e da come essi vengono utilizzati e gestiti. Se le distinte base sono errate, se le specifiche di controllo non vengono versionate in modo rigoroso o se non vi è un meccanismo affidabile per la gestione delle modifiche, l’integrazione finisce per amplificare gli errori invece di risolverli. Implementare una vera e propria strategia di data governance si rivela perciò essenziale. Lo scenario ideale si basa sull’integrazione dei flussi, e non dei dati. Le buone pratiche per migliorare la qualità dei dati per questo prevedono la definizione di una fonte autorevole: nel PLM si creano e gestiscono i componenti tecnici, nell’ERP si arricchiscono le informazioni contabili e di costo, mentre il MES monitora l’esecuzione e i consumi in officina. Così da evitare che più sistemi differenti gestiscano i medesimi dati in un determinato momento. A questo si affianca la gestione ottimizzata delle modifiche (change management) per monitorare e approvare ogni revisione progettuale o di processo, con impatti chiari sulle distinte base, i piani di produzione e i documenti di qualità. Infine, una fase di validazione e pulizia costante dei database previene l’accumulo di duplicati e dati obsoleti, rendendo i flussi di lavoro più robusti e affidabili. In un contesto destinato a crescere in complessità, l’attenzione alla correttezza e all’affidabilità dei dati – anche in relazione ai processi in cui questi sono poi utilizzati – diventa allora un elemento critico di successo. Questo aspetto garantisce visibilità end-to-end sui processi, riduce al minimo gli errori e rende più agile reagire alle spinte del mercato.
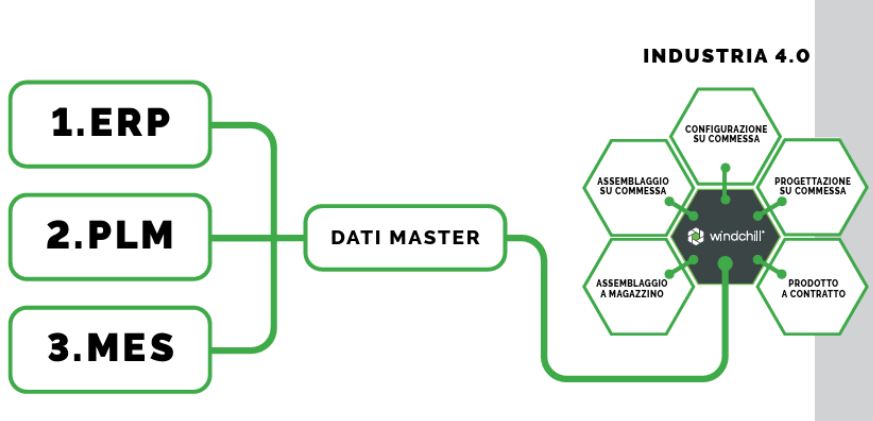
I benefici di un sistema connesso
Integrare in modo sinergico PLM, ERP e MES, all’interno di un ecosistema in cui ciascun sistema si occupa in modo specifico dei propri ambiti, comporta notevoli vantaggi per le aziende manifatturiere. Uno dei principali benefici consiste nella riduzione dei costi e degli sprechi, che si ottiene grazie all’abbattimento delle discrepanze tra ingegneria e “officina”, all’ottimizzazione dell’uso dei materiali e a un controllo più accurato della supply chain. Quando la comunicazione tra i vari reparti è fluida e automatizzata, risulta anche più semplice intervenire tempestivamente laddove emergano difetti di progettazione o difformità nelle linee di produzione, evitando di portare avanti lavorazioni errate o di accumulare scorte in eccesso. A questo si aggiunge la possibilità di tracciare con precisione ogni passaggio, così che eventuali richiami o sostituzioni siano più mirati e meno dispendiosi in termini di tempo e risorse.
Un sistema connesso porta anche a un netto miglioramento dell’efficienza e a una riduzione del time-to-market. Laddove progettisti e operatori di fabbrica abbiano accesso a un archivio unificato di informazioni, ogni modifica sui disegni di prodotto può essere trasmessa in tempo reale alle linee di produzione, che reagiscono rapidamente senza necessità di inserimenti manuali o passaggi intermedi. Tale meccanismo consente di evitare ritardi, incomprensioni e rallentamenti, permettendo di rispondere in maniera dinamica alle mutevoli condizioni di domanda o alle richieste specifiche di un cliente.
La qualità dei prodotti, inoltre, beneficia di questa integrazione poiché gli operatori possono basarsi su dati sempre aggiornati e su istruzioni di lavoro dettagliate, derivanti dalle distinte base e dai modelli tridimensionali caricati nel PLM. Il MES è in grado di monitorare costantemente i parametri di produzione, segnalando qualsiasi scostamento in tempo reale e facilitando l’implementazione di azioni correttive immediate. Questa sinergia rende più semplice documentare e tracciare ogni variazione o intervento, con ricadute positive anche sulle attività di verifica o certificazione, sempre più rilevanti in un mercato che guarda con grande attenzione alla conformità e all’affidabilità del prodotto.
Da ultimo, occorre sottolineare come il sistema connesso risulti flessibile e scalabile. Le aziende possono infatti introdurre varianti di prodotto o apportare modifiche ai processi senza stravolgere l’intera infrastruttura informativa, grazie a un digital thread che aggiorna ogni reparto in maniera coordinata. Tali funzionalità rendono anche più agevole l’eventuale adozione di piattaforme Industrial IoT, di analisi avanzata o di tecnologie immersive (come la realtà aumentata), ponendo le basi per una fabbrica sempre più digitale, connessa e orientata all’innovazione.
Un approccio graduale all’integrazione
Benché i vantaggi descritti siano evidenti, è importante sottolineare che un progetto di integrazione tra PLM, ERP e MES può risultare articolato, specialmente in realtà di grandi dimensioni o con stabilimenti distribuiti. Un metodo raccomandato prevede di procedere in modo iterativo e graduale, individuando innanzitutto i flussi prioritari (come il trasferimento delle informazioni sulle parti fabbricate dal PLM all’ERP) e costruendo un primo livello di interfaccia. In questa fase iniziale, si verifica il corretto funzionamento dei processi, si raccolgono feedback dai reparti e si correggono eventuali anomalie o duplicazioni. Una volta validata la soluzione, si procede a espandere il perimetro dell’integrazione. A poco a poco, vengono inclusi nel progetto il cambio di versioni, la gestione estesa della distinta base di fabbricazione e l’interfacciamento con il MES. Grazie a questo metodo basto su apprendimento e adattamento, il team IT e i referenti di processo possono acquisire piena consapevolezza degli strumenti e maturare la best practice necessaria a costruire, passo dopo passo, il digital thread di cui l’azienda necessita.
Digital thread, oltre Industria 4.0
Una volta costruito un ecosistema PLM/ERP/MES coerente e connesso, le aziende possono estendere il progetto a iniziative di trasformazione digitale più ampie. L’Industrial Internet of Things (IIoT) permette, ad esempio, di connettere sensori, macchinari e dispositivi in rete, raccogliendo in tempo reale dati utili per analisi e ottimizzazione dei processi. Tali informazioni possono fluire all’interno del digital thread del prodotto, supportando miglioramenti continui. Una piattaforma così strutturata abilita il monitoraggio in tempo reale dell’efficienza degli impianti (Oee), rende possibili interventi di manutenzione predittiva, abilita i vantaggi delle tecnologie digital twin, e offre alle linee produttive strumenti di analisi avanzata, in grado di suggerire azioni correttive sulla base di trend o anomalie rilevati dai sensori. Allo stesso modo, l’uso dell’intelligenza artificiale in fase di produzione può fornire insight su come modificare parametri o sequenze operative per ottenere una resa più elevata, riducendo gli scarti. Il risultato finale è un ambiente produttivo “intelligente”, dove le decisioni automatizzate si basano su un archivio di dati unico, coerente e completo, garantito dall’integrazione tra PLM, ERP e MES.
Per saperne di più scarica il whitepaper: Guida ai sistemi connessi nella produzione manifatturiera
Non perdere tutti gli approfondimenti della Room Manufacturing: Sistemi Connessi e Dati Unici by PTC
© RIPRODUZIONE RISERVATA