La sostenibilità ha bisogno delle tecnologie che permettano di studiare, prima, e realizzare poi progetti efficaci per ridurre l’impronta ecologica. Spesso le aziende impegnate in questa direzione agiscono con un respiro ancora più ampio, tenendo presenti tutti gli obiettivi di Agenda 2030 che comprendono anche quelli relativi a inclusione, tutela delle diversità, etc. Di fatto la “sostenibilità” a tutto tondo dovrebbe diventare parte integrante dei modelli di business, un tema filo conduttore anche in occasione degli ST Sustainability Days organizzati da STMicroelectronics.
L’azienda fornisce soluzioni a semiconduttore che possono contribuire a risolvere sfide ambientali e sociali, inoltre lavora per ridurre al minimo la sua impronta ambientale complessiva e prosegue il suo impegno per diventare carbon neutral entro il 2027.
Nel solco degli obiettivi di Agenda 2030 è impegnata a generare un ambiente più sicuro, inclusivo per le persone e nella promozione dell’istruzione nel campo delle discipline Stem. L’evento ST Sustanibility Days ha rappresentato, soprattutto, l’occasione per presentare soluzioni, iniziative e idee innovative per un futuro sostenibile, insieme ai partner. Ad animare l’iniziativa l’idea secondo la quale occorre unire le forze per creare ecosistemi win-win in grado di guidare un cambiamento sistemico.
E proprio dall’unione di queste forze abbiamo attinto scegliendo un paio di casi a nostro avviso tra i più significativi ed originali.
Smart agricolture
Si chiama Talking Plant il progetto di smart agricolture portato avanti da un gruppo di “stakeholder” costituito da Luisa Fracassini, Sustainability & Open Innovation manager, e Roberto La Rosa, progettista di sistemi energeticamente autonomi e sensori wireless smart a basso consumo. Entrambi di ST, gli esperti sono stati accompagnati nel viaggio dal professore Davide Brunelli del Dipartimento di Ingegneria Industriale dell’Università di Trento, che svolge ricerca su sistemi “embedded” ultra low-power applicati all’agricoltura. Un viaggio che ora proseguirà con l’istituto tecnico G. Marconi di Dalmine, nel bergamasco (che sperimenterà sul campo il prototipo), e due aziende: Ribetech, che realizza pannelli solari flessibili per IoT, e Check-up, per l’industrializzazione del caso.
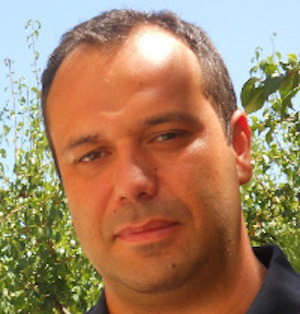
Il progetto nasce con l’obiettivo ambizioso di consentire alle piante di “fornire dati” agli agricoltori in un dialogo costante grazie alla possibilità di sfruttare l’energia dei microbi del terreno per alimentare specifici sensori a bassa potenza. Sembra fantascienza, ma non lo è. La Rosa spiega come da tempo STMicroelectronics è al lavoro su una piattaforma, Bftag (Battery Free Tag) per la realizzazione di sensori senza fili che siano anche in grado di alimentarsi senza batterie, così da ridurre al minimo la manutenzione. “Facile quando c’è la disponibilità del sole, ma grazie al professor Brunelli – specifica La Rosa – si è studiata la possibilità di estrarre energia dal terreno, una fonte perpetua che permette di avere anche informazioni sulla salute del suolo e della pianta”.
In questo caso a fornire energia sono colonie di batteri che producono naturalmente degli elettroni che due elettrodi nel terreno raccolgono e utilizzano come sorgente di energia. Le colonie si nutrono grazie alle stesse piante coltivate ed inoltre forniscono parametri sulla qualità del terreno, sull’umidità e il benessere della pianta. Questo consente di ridurre i costi e soprattutto di poter utilizzare sensori con un minimo dispendio di risorse anche nella pianificazione dell’attività. Solo per scendere un poco di più nel dettaglio l’energia è prodotta dalla Fuel Cell Microbica (Mfc), che genera una corrente molto, molto bassa che alimenta la tecnologia elettronica di ST. A che punto siamo: oggi è disponibile come prototipo un piccolo kit autosufficiente in vaso. Comprende i sensori smart di ultima generazione e la Fuel Cell Microbica di Brunelli. La piattaforma Bftag sfrutta due sensori specifici per misurare l’umidità e la temperatura.
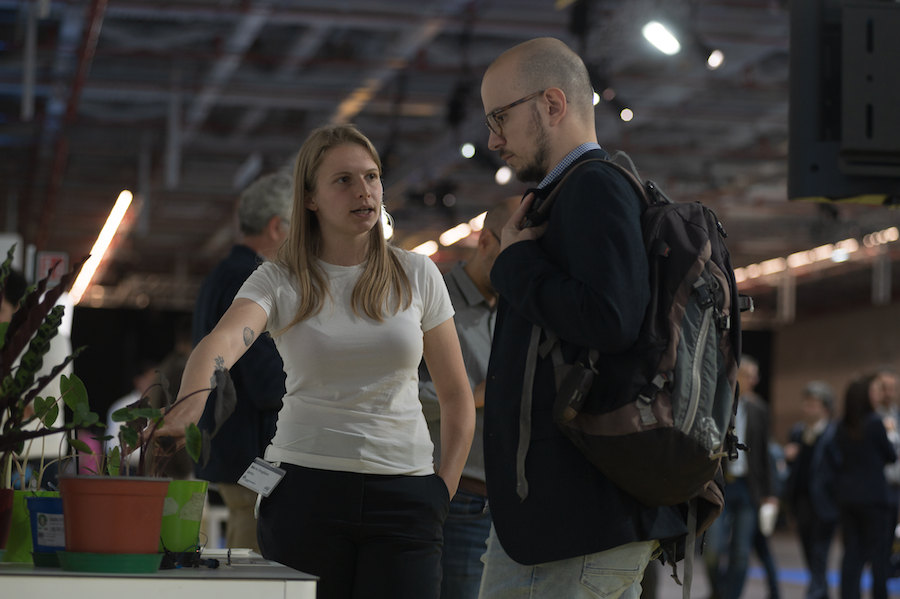
Nel caso in cui la platform sia alimentata dalla cella solare è possibile ovviamente misurare anche la luminosità ambientale, nel caso sia alimentata dalla fuel cell si ottengono i dati anche sulla qualità del terreno e indirettamente sulla salute della pianta. In tutti i casi i coltivatori dispongono delle informazioni necessarie per verificare lo stato di salute di terreno e piante, decidere quindi come intervenire o semplicemente quando irrigare e tutto attraverso un’app utilizzabile direttamente con lo smartphone.
Il prossimo passaggio prevede di passare dalla sperimentazione in vaso all’effettivo utilizzo “sul campo”. Inizialmente quello dell’Istituto Marconi e poi in una piccola smart farm fino all’industrializzazione, fase in cui interviene il contributo di Check-up.
Il ciclo dell’acqua
Riguarda ancora più direttamente STMicroelectronics il secondo caso di studio che scegliamo proprio in relazione all’attualità del tema, ovvero il “riciclo” ed il riutilizzo degli scarti di quello che oggi, non a caso, è già definito “oro blu”: l’acqua. “La premessa che dobbiamo fare è che un’azienda di microelettronica ha un forte bisogno di acqua – spiega Cinzia Quartini, Water & Eco facilities manager del sito di Agrate – e il solo sito di Agrate necessita mediamente di 400 metri cubi di acqua ogni ora”.
Serve per rimuovere impurità dai wafer da cui nasceranno i microchip, oltre che per raffreddare i macchinari, mantenere stabili le temperature degli impianti e per l’utilizzo da parte dei dipendenti (oltre 5.000 le presenze on-site nell’arco delle 24 ore). Di tutta l’acqua utilizzata, solo il 2% è necessario sia potabile. Ed è questa la percentuale attinta dalla rete idrica comunale. La percentuale rimanente è attinta, invece, direttamente da undici diversi pozzi.
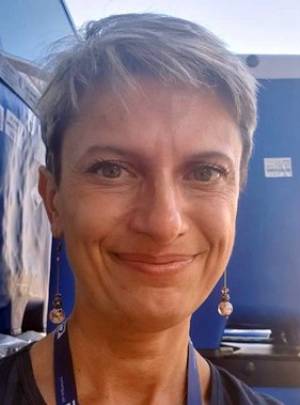
Si parla quindi di acqua di falda che viene incanalata al 30% per un utilizzo non primariamente industriale, mentre il restante 70% confluisce negli impianti di produzione di acqua ultrapura – denominati con l’acronimo inglese Upw (UltraPure Water) e quindi è destinata ad essere utilizzata per il risciacquo dei wafer. Prosegue Quartini: “In questo caso l’acqua viene lavorata per osmosi, ovvero il filtraggio (a pressione) sempre più serrato dell’acqua fino ad eliminarvi l’organico e ottenere un composto in purezza”.
Per quanto riguarda questo specifico punto l’azienda sta pensando alla sostituzione degli impianti di osmosi attuali, basati su membrane filtranti in acetato di cellulosa, con sistemi di purificazione basati su membrane in poliammide, perché consentono di estrarre dall’acqua grezza ben il 98% di acqua ultrapura, generando solo il 2% di scarti, che verrebbero poi comunque recuperati. Allo stato attuale, invece, lo scarto è maggiore. Dopo la lavorazione, in ogni caso, l’acqua viene incanalata verso i reparti produttivi dove può essere impiegata per lavare i wafer al fine di eliminare impurità chimiche e particellari senza alterarne o danneggiarne la superficie.
Il problema si pone quindi proprio nella fase in cui è necessario rendere pura l’acqua, perché il processo di osmosi inversa sottrae ioni le particelle e il materiale organico ma genera anche scarti (circa il 25% dell’acqua). La metà dello scarto dell’acqua in precedenza inviata al processo di filtraggio viene trattata in profondità per ritornare acqua grezza da ultrapurificare di nuovo, mentre l’altra metà viene instradata ad un serbatoio che la indirizza a utenze secondarie. Solo la parte non più riutilizzabile viene inviata agli impianti di trattamento waste water. L’obiettivo ora, spiega Quartini, è “utilizzare la waste water per produrre acqua grezza in modo tale da avvicinarci fino al 70% di riutilizzo”, mentre oggi si parla di un sistema di recupero e trattamento dell’acqua che permette di ridurre del 42% l’utilizzo di acqua di falda.
© RIPRODUZIONE RISERVATA