L’evoluzione del manufacturing verso il modello di Industria 4.0 porta in primo piano il tema della componentistica intelligente e della manutenzione predittiva. Impianti e macchinari devono oggi essere pensati e sviluppati nell’ottica di efficientamento dei processi, per garantire la massima durata nel tempo, migliorare la qualità dei prodotti e ridurne i costi.
In qualità di fornitore globale di soluzioni per l’intralogistica e la movimentazione di materiali, che sullo sviluppo di questi processi fonda il proprio modello industriale, Interroll vive in modo diretto queste dinamiche.
Ce ne parla Claudio Carnino, direttore commerciale e country speaker di Interroll Italia, nell’ambito di un seminario organizzato a Milano con l’obiettivo di facilitare la comprensione dello stato dell’arte e fare cultura sulla manifattura predittiva.
“Vogliamo essere protagonisti del mondo Industria 4.0 e della logistica attraverso progetti innovativi – esordisce il manager – e negli ultimi anni abbiamo risposto concretamente con investimenti in questa direzione, intraprendendo la strada della componentistica intelligente per realizzare sistemi ad alte prestazioni, personalizzati e integrabili nelle applicazioni in ottica 4.0”.
Basata in Svizzera, Interroll conta oggi 2.300 dipendenti distribuiti in oltre trenta società a livello mondiale e affida la propria produzione, ricerca e sviluppo a sette centri globali.
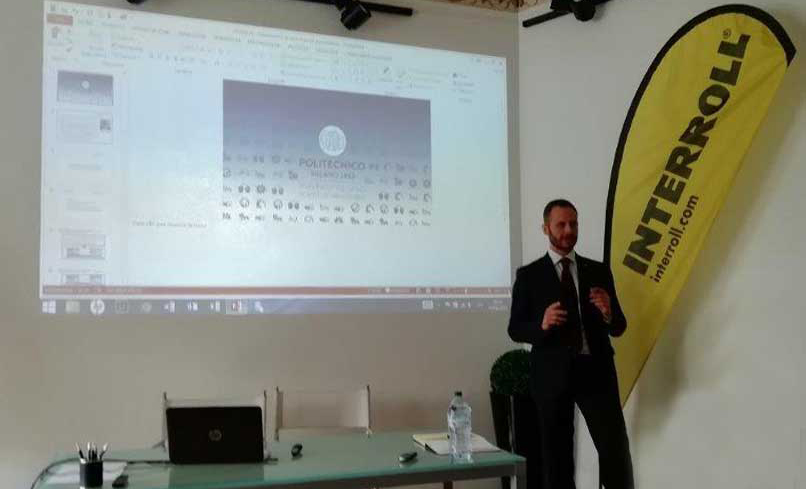
“Le esigenze dell’automazione industriale non sono oggi più esclusivamente legate alla velocità dei flussi, piuttosto che alla capacità degli impianti di gestire gli scambi nella loro complessità. Ormai si parla di dati, informazioni e diagnostica in ottica di massima flessibilità e minimalizzazione delle perdite per manutenzioni da guasto – spiega Carnino -. Il 2019 rappresenta un anno importante per Interroll, che prosegue sulla strada della componentistica intelligente attraverso una nuova soluzione, DC Platform, che gestisce motorulli e schede legate alla movimentazione 24 volt ampliando la gamma di prestazioni per rispondere alle esigenze di raccolta e analisi dei dati legati alla manutenzione predittiva. Le parti meccaniche si parlano e sono in grado di immagazzinare dati e raggrupparli, analizzarli e scambiarli con altri sistemi; una chiave essenziale ed esigenza imprescindibile per poter diminuire al massimo i tempi di fermo macchina per la manutenzione, che rappresentano oggi costi immensi per le aziende”.
Manutenzione, progettazione a inizio vita
A dare un contributo accademico al tema è Marco Macchi, professore ordinario presso il dipartimento di ingegneria gestionale del Politecnico di Milano, che analizza le tendenze a venire nel mondo della manutenzione predittiva.
Nel cambiamento paradigmatico della quarta rivoluzione industriale, si assiste allo spostamento da manutenzione correttiva a manutenzione predittiva, è il concetto chiave introdotto da Macchi: “Un buon investimento viene ripagato nel tempo attraverso la manutenzione, ma questa deve andare di pari passo con la progettazione all’inizio della vita, pensando al ciclo di utilizzo del prodotto in chiave strategica”, spiega Macchi.
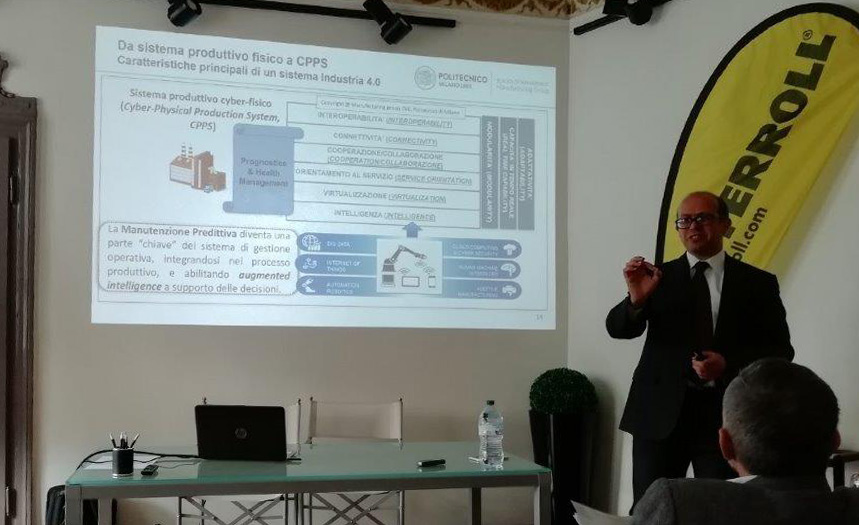
“La manutenzione avanzata – prosegue il docente – gioca un ruolo importante per la digitalizzazione in ottica Industria 4.0, quel processo che mi piace chiamare più evoluzione che rivoluzione: un connubio di tecnologie che evolve e viene a maturità facendo evolvere l’intero sistema. In questo senso la manutenzione è adattativa, si fa in tempo reale, non è stampata sulla pietra. La manutenzione si intreccia infatti con l’evoluzione stessa delle logiche di produzione dell’asset. Nel momento in cui un prodotto o un bene durevole viene progettato, la manutenibilità dello stesso è un investimento di garanzia nel tempo, perché non copre semplicemente le falle ma guarda al lungo termine grazie alla riduzione degli interventi di riparazione, alla capacità di predire anomalie e degradi di prestazione, in modo da limitare gli impatti sui diversi stakeholder interessati. Un percorso ideale a garanzia del valore aggiunto del prodotto e dell’impianto”.
Si fa così strada la “vision adattativa”, dove le parole chiave sono: capacità prognostica, col fine ultimo di mitigare i rischi di sistema e anticipare l’accadimento dei guasti; multidisciplinarità e interoperabilità, fondamentali per avere componendi che dialogano tra loro con una serie di funzionalità sia fisiche che di spazio cyber-fisico; diagnostica, ovvero la codifica dello stato di salute, come punto intermedio per arrivare alla prognosi del guasto.
Manca una figura chiave
Capacità di fare sistema, cooperazione e collaborazione sono parallelamente indispensabili per generare valore verso il business che giustifichi non solo il costo ma porti valore aggiunto ai processi del manifatturiero.
In questo contesto, si segnala nel corso dell’evento la mancanza di una qualifica ingegneristica specifica in ambito manutentivo, nuova figura “che deve diventare sia tecnica che gestionale – spiega Macchi – con la capacità di predire anomalie e degradi di prestazione, monitorare gli asset industriali e fare sorveglianza per anticipare i possibili fermi e guasti (non solo sul sintomo ma anche sull’utilizzo in senso ampio), che conosca il corretto uso degli impianti, anche se non vicini al degrado, che sappia fare monitoraggio delle condizioni nel corso della vita con estensione della vista stessa”.
© RIPRODUZIONE RISERVATA