“Additive manufacturing è il modello produttivo per cui si aggiunge materia là dove serve (e non viene invece tolta quella che non serve, come prevede il modello sottrattivo). Aziende, università, innovation center, Its, ma anche Pmi hanno compreso le potenzialità ben espresse dal termine stesso e il nostro Paese non è certo fanalino di coda. Nella fase storica che stiamo vivendo però è anche importante che ci siano realtà in grado di fare da capofila. General Motors, Leonardo, Wärtsilä, Istituto nazionale di Fisica Nucleare di Padova, Brembo sono tra queste e già hanno adottato le tecnologie di additive manufacturing”.
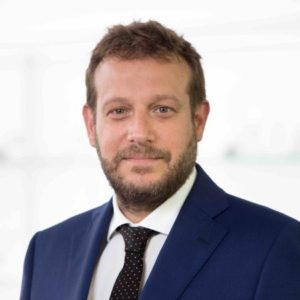
Così Giancarlo Scianatico, direttore generale di Eos Italia, apre la giornata di riflessione sullo “stato dell’arte” e sul futuro dell’additive manufacturing (AM), e saluta le aziende (italiane e non) presenti.
E proprio il confronto è lo scopo della manifestazione che Eos ha organizzato al Kilometro Rosso con la partecipazione di oltre 250 persone. Prosegue Scianatico: “In Italia la tecnologia AM è stata decretata dal mondo industriale come destinata a stravolgere i modelli classici di progettazione, produzione e supply chain e parte integrante della rivoluzione industriale 4.0. L’Additive può davvero rappresentare un “pennello al servizio della creatività del Paese per realizzare nuove forme””.
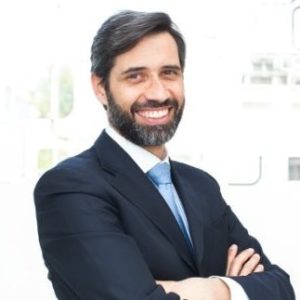
Salvatore Majorana, direttore del Kilometro Rosso, gli fa eco e aggiunge alla giornata un tema di riflessione: “Oltre la linea del Kilometro Rosso spesso la gente non sa cosa succede, e invece la nostra missione è semplice: creare con il parco scientifico (nodo di una rete aperta) collegamenti tra impresa e ricerca; realizzare prossimità fisica e progettuale anche tra le aziende, far parlare tra loro le realtà. Perché quando si confronta in modo costruttivo l’Italia offre il meglio delle proprie potenzialità. Per questo è naturale ospitare una comunità industriale, quella del manifatturiero, che esprime nel mondo la capacità del Paese di saper fare bene le cose”.
La vera sfida tecnologica in verità è riuscire ad indirizzare gli sforzi dove l’Additive Manufacturing può effettivamente offrire il meglio delle sue possibilità per esempio rigenerando in modo massivo le logiche di progettazione. E farlo sulla base di cinque passaggi chiave: Da dove cominciare? Quando entrare in produzione? Come impostare la digital AM factory? Come crescere? Come immaginare il futuro produttivo sulla base dell’AM? Domande non facili cui rispondere, tanto che a distanza di circa 30 anni dai primissimi tentativi di stampa 3D vediamo come la tecnologia abbia corso molto più della capacità di integrarla effettivamente in produzione.
Al centro per Eos, in questa fase, c’è la proposta laser sintering, che nel prossimo futuro permetterà maggiore scalabilità, la stampa di oggetti di maggiori ingombri e una scelta di materiali sempre più alta.
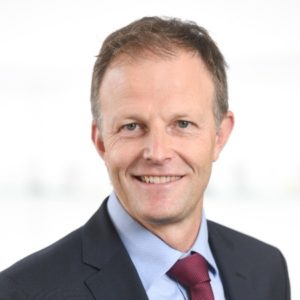
Ne parla Thomas Weitlaner, business development director Eos: “L’azienda (presente in 15 Paesi con ricavi complessivi per circa 350 milioni di euro, per 3500 sistemi Eos installati) prevede per la prossima generazione di sistemi di AM importanti evoluzioni nel 3D printing con una ampia scelta di polveri metalliche (si inizia a lavorare bene sul rame), una progressiva automazione di ogni processo, scalabilità, integrazione nella supply chain produttiva e risparmio dei costi anche fino al 50%”. Weitlaner sottolinea però anche l’estensione delle tecnologie AM in altri ambiti di produzione – per esempio healthcare e efficientamento energetico, dopo automotive e aeronautica, – e con tecnologie 4.0 integrate, a partire dalle piattaforme Iiot (Industrial IoT).
La risposta alle altre domande “di metodo” arriva direttamente dall’esperienza delle aziende presenti che lavorano sfruttando l’AM.
Ripensare progettazione e processi
In primis da Giuseppe Saragò, director manufacturing excellence di Wärtsilä (motori e soluzioni per il settore marino e energy). Spiega Saragò: “Operiamo in un ambito in cui i componenti hanno importanti dimensioni, è evidente che pensare all’AM è sfidante. Ci abbiamo provato dal 2010, tra successi e fallimenti (con sperimentazioni su ricambi e prototipazioni), eravamo quasi a un passo dal riconoscere che l’AM non si sarebbe mai adattato a questa industria”.
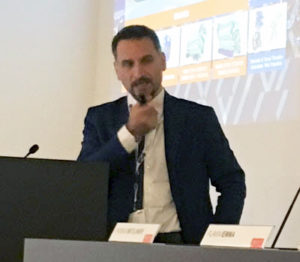
I fallimenti hanno portato invece alla lezione più importante, Saragò: “L’approccio all’additive non riguarda le tecnologie, è sbagliato rispondere alla domanda “come produco quello che ho”. Bisogna rispondere alla domanda “cosa sto cercando di fare, quali funzionalità nuove voglio realizzare””.
Quindi un approccio virtuoso deve riguardare invece l’analisi delle potenzialità di design freedom (possibilità di ripensare completamente la progettazione) dell’AM che è una tecnologia intrinsecamente digitale, con possibilità di crescita potenziali illimitate, date dalla combinazione di tante tecnologie e dalla mole di dati a disposizione.
Combinare tecnologie e competenze
Serve un approccio smart, volto a comprendere come combinare insieme le tecnologie additive per realizzare esattamente ciò di cui si ha bisogno. E’ tutt’altra prospettiva rispetto al chiedersi se è meglio produrre in AM solo prototipi e parti di ricambio o componenti strategiche in volume.
Ritorna il tema cardine: “Anche nell’ambito dell’AM diventare 4.0 significa capire come bisogna cambiare e ripensare i processi. I pilastri sono quindi: re-thinking design che significa chiedersi perché e cosa si ha bisogno davvero di stampare, quali sono le funzionalità che altrimenti non possono essere ottenute, come si possono eliminare i limiti di quello di cui si dispone, o massimizzarne i vantaggi”. Da qui la capacità di “lasciare contaminare le competenze dei giovani con l’esperienza, che vuol dire sperimentare fissando però degli obiettivi, ma anche accettare e favorire la contaminazione di vecchie tecnologie manifatturiere con le nuove. E lo stesso deve accadere tra le aziende, quindi bisogna saper abbracciare quella che gli esperti chiamano cross-company collaboration“.
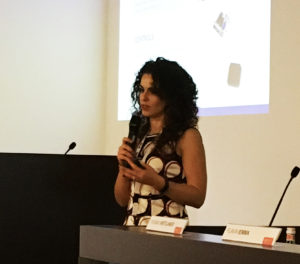
Questo è il filo rosso che lega l’esperienza di Wärtsilä a quella del centro di competenze di Torino di General Motors. Flavia Iemma, pre-production analyst e additive manufacturing buyer: “Nella nostra esperienza abbiamo individuato una serie di vantaggi dati dall’AM, dalla riduzione dei tempi di sviluppo, a una maggiore libertà nel design, poi la possibilità di consolidare il numero di parti, ridurre i costi e la complessità della supply chain e un minore impatto aziendale”.
La fase di sperimentazione sia con materiali plastici sia di metallo è importante, ma secondo Iemma: “Oltre l’ottimizzazione di processo è fondamentale pensare all’integrazione dei progetti in linea di produzione e comprendere in quali contesti determinati componenti determineranno dei vantaggi significativi se prodotti con l’AM, anche cambiando i materiali di produzione se necessario”. Un punto resta fermo: “Progettare una turbina per la produzione con tecnologie AM così come si sarebbe progettata prima non ha alcun senso”. Obiettivo ora di GM è di lavorare sulla ricerca di quali componenti offrano effettivi vantaggi in produzione AM, anche nell’ottica di consolidarne il numero.
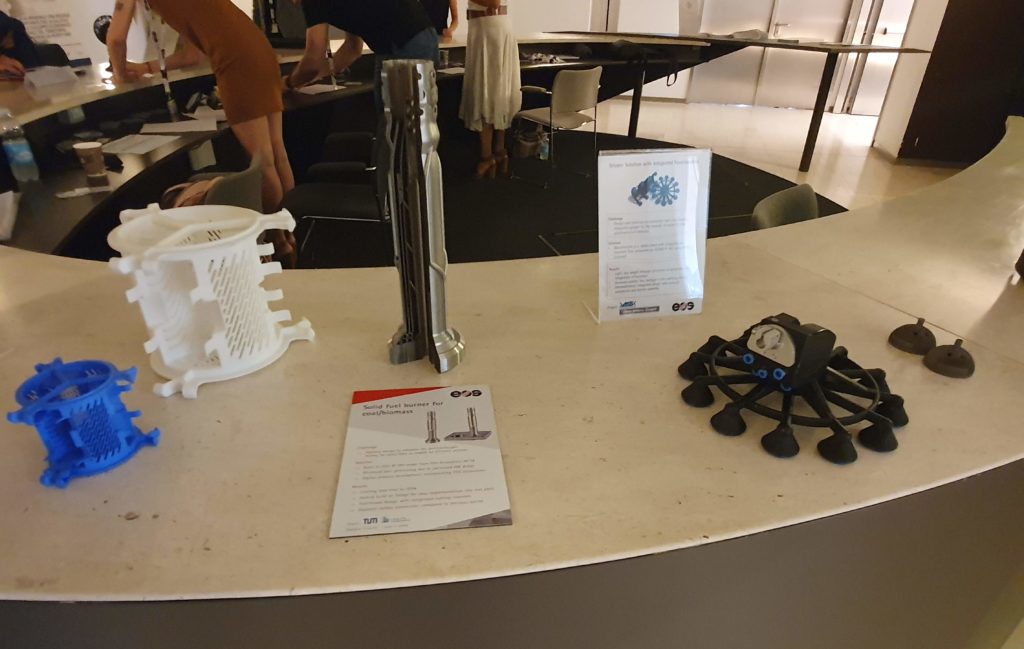
Le criticità
Non si tratta di immaginare il manifatturiero convertito all’Additive Manufacturing, quanto piuttosto di come sfruttare le possibilità offerte per migliorare la produzione. Anche perché non mancano alcune criticità tra cui quella relativa a determinate certificazioni del prodotto finale, possibili nella produzione di parti critiche con il metodo sottrattivo, ma oggi non ottenibili tramite AM, per cui invece sono già disponibili certificazioni appropriate ma solo sulla materia prima (per esempio le polveri).
Nell’esperienza di Leonardo (produzione di elicotteri), per esempio, l’AM non è utilizzato per componenti di carico critiche. Non solo, il vendor sottolinea l’importanza di approfondire il tema dei controlli non distruttivi in relazione all’AM (che ora costituiscono caso per caso un tema a parte), mentre la normativa è ancora in fase di parto. Tra certificazioni e potenzialità tecnologiche c’è ancora scollamento.
Tra i temi caldi della giornata anche la protezione della proprietà intellettuale. Se infatti tra in vantaggi evidenti dell’Additive Manufacturing vi sono la possibilità di passare dal progetto Cad 3D direttamente in produzione, originando pezzi anche molto complessi con grande precisione, in tempi rapidi – con una sola macchina in grado di realizzare più prodotti completi, finiti, con un numero inferiore di parti – tra gli svantaggi c’è la maggior facilità di pratiche di concorrenza sleale.
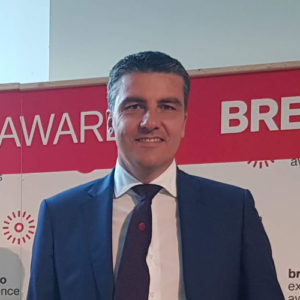
Paolo Rezzaghi, Ipr manager di Brembo (produzione pinze per i freni in ambito automotive), sottolinea alcune criticità a partire dalla “facilità di contraffazione con la sola disponibilità di un’apparecchiatura e di un file Cad, facilmente reperibile in rete. Conseguenza per certi aspetti naturale, ma non per questo ineluttabile di quella che può essere definita come la “democratizzazione della manifatturazione” che sfuoca le differenze tra produttore, distributore e utente finale”.
Tra le possibili soluzioni al problema, in un contesto – quello italiano – dal punto di vista legislativo comunque ben attrezzato grazie alla Regolamentazione 2017/2007 (Ini) e al Codice della Proprietà Industriale D.Lgs. n.30 del 10 febbraio 2005, Brembo sottolinea l’introduzione di misure di protezione che permettano un utilizzo limitato dei file (crittografia, codici di sicurezza) e la verifica in tempo reale dell’utilizzo, anche online.
© RIPRODUZIONE RISERVATA