Con urgenza sempre maggiore si sente parlare del bisogno di ridurre i consumi di materie plastiche. Meno parole si spendono invece per spiegare che, per più di 30 anni da quando si è iniziato ad utilizzare questo materiale, che ha rivoluzionato letteralmente le abitudini e l’industria, la maggior parte dei Paesi sviluppati ha spedito i propri rifiuti nei Paesi asiatici, e la Cina è stato il maggiore importatore. Europa e Italia sono state costrette a porsi il problema perché nel 2013 è entrato in vigore il protocollo Green Fence e il governo di Pechino ha avviato ispezioni sui carichi in arrivo; dal 2017, e poi con il National Sword, la Cina ha iniziato a vietare in modo ancora più severo l’importazione anche di altri materiali e l’esportazione si è spostata in altri Paesi.
Il problema
Oggi lo stop all’importazione da parte della Cina è definitivo, e le prossime scadenze – la più vicina quella del 2021 – imporranno ai Paesi UE addirittura l’obbligo di notifica per vendere plastica mista all’interno dei confini europei. In numeri: dal 1980 al 2013 si sono esportate da 0 a 55 milioni di tonnellate e in sei anni, dal 2013 al 2019, la cifra è tornata prossima allo zero (solo 8 milioni di tonnellate).
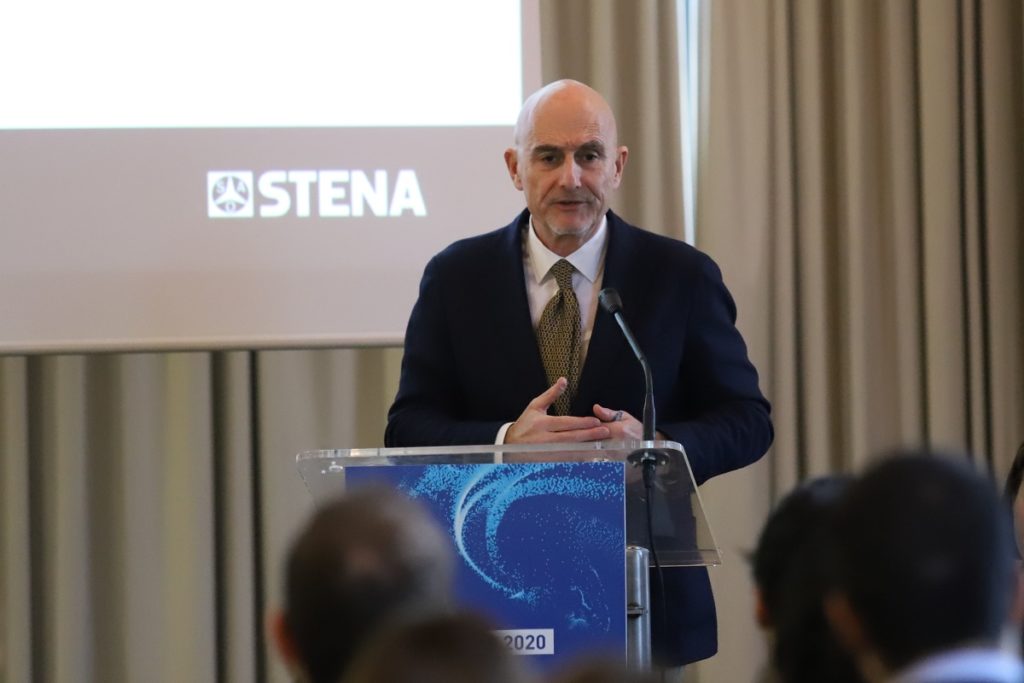
“Quasi 40 anni di inattività nella ricerca sulle possibilità di riciclo si pagano ora. Non ci si è preoccupati di elaborare norme praticabili per le plastiche da riciclo e si è investito poco”, spiega Giuseppe Piardi, managing director, Stena Recycling, introducendo l’analisi del progetto per lo studio delle innovazioni di processo e miglioramento delle percentuali di riciclo e recupero delle plastiche contenute nei rifiuti Raee del raggruppamento 4, ovvero i piccoli elettrodomestici e i rifiuti elettronici. Il progetto, tra febbraio 2018 e gennaio 2020, è stato realizzato in collaborazione con il Ministero dell’Ambiente e della Tutela del Territorio e del Mare, ed ha visto la collaborazione di Ecolight, Stena Recycling e dell’Università di Brescia.
Ecolight è tra i maggiori collettivi che in Italia si occupano della gestione dei Raee, e conta quasi 1.900 aziende consorziate. Assicura la gestione e lo smaltimento di pile e accumulatori in una logica di sviluppo sostenibile, e nel corso del 2019 ha gestito 22.500 tonnellate di rifiuti da apparecchiature elettroniche, mandando a trattamento 15.000 tonnellate di rifiuti del gruppo R4, quello di cui si parla.
Il collettivo serve la Gdo, in relazioni agli obblighi di legge vigenti sul ritiro dell’usato, ed ha effettuato oltre 4.800 ritiri dai punti vendita. Il contesto è sfidante, come spiega, Giancarlo Dezio, direttore generale del consorzio: “La responsabilità del produttore nel tempo sembra destinata a crescere anche in relazione agli aggiornamenti del D. Lgs.152, (in bozza). Gli obiettivi di raccolta, di recupero e di riciclaggio nel tempo dovranno di conseguenza necessariamente migliorare”. Infatti la bozza preannuncia: “]…[i produttori finanziano e organizzano sistemi di raccolta in grado di conseguire gli obiettivi minimi di recupero e riciclaggio”, con un impegno quindi più significativo sottolineato dalle righe secondo cui “i produttori di Aee adempiono agli obblighi mediante sistemi di gestione individuali e collettivi, sostenendone i relativi costi…Ciascun sistema collettivo garantisce il ritiro di Raee da ogni luogo di raccolta su tutto il territorio nazionale secondo le indicazioni del centro di coordinamento”.
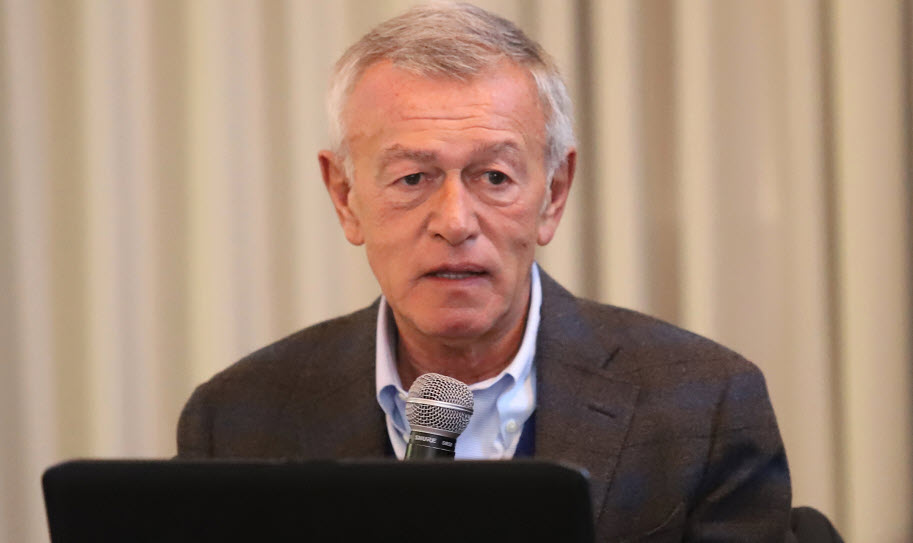
Sulla possibilità e sulle prospettive per innescare un sistema virtuoso di economia circolare per gli impianti di trattamento Raee, torna Piardi che spiega come “mentre per alcuni materiali come ferro, alluminio, rame, gli impianti hanno maturato oggi una grande esperienza, frutto anche di importanti investimenti e di regolamenti di ben più antica data, per le materie plastiche ci troviamo di fronte a vuoti legislativi, norme in parte inapplicabili perché non sono specifiche per le materie plastiche, e presenza di componenti pericolosi come i ritardanti di fiamma da intercettare e da distruggere”. Non solo, l’economia circolare per la plastica significa necessariamente pensare al reimpiego in applicazioni diverse rispetto alle originarie. Quindi un “loop di suo difficile da chiudere – chiude Piardi – su cui servono gli sforzi congiunti con la ricerca”.
Il progetto
In questo contesto, Stena Recycling Italia, che fa parte del gruppo internazionale svedese Stena Metall, ed è specializzata nel settore del riciclo dei rifiuti da apparecchiature elettroniche (sedi in Brianza e a Verona), con Ecolight e il Dipartimento di Ingegneria Meccanica e Industriale dell’Università degli Studi di Brescia avvia il progetto ora appena concluso.
Negli anni della ricerca vengono prese in considerazione le plastiche dei piccoli elettrodomestici e dell’elettronica di consumo (Raee R4), che costituiscono circa il 30% del materiale di quei prodotti. Si tratta di materiali caratterizzati dalla molteplicità dei polimeri e dalla presenza dei ritardanti di fiamma bromurati, che non possono essere recuperati ma vanno inceneriti. Consorzio (Ecolight), Ricerca (Università di Brescia) e Industria (Stena) si pongono come obiettivo l’individuazione di nuove tecnologie che possano migliorare i processi di separazione dei componenti riutilizzabili da quelli da eliminare per potenziare la filiera Raee ed in particolare l’apporto all’economia circolare dei rifiuti elettronici.
Il metodo
I rifiuti Raee sono sottoposti al consueto processo di trattamento previsto da Stena, quindi il loro trattamento inizia con una prima fase di “apertura dei singoli rifiuti” (procedimento meccanico), che segue quella di accoglienza dopo la raccolta dalle isole ecologiche o dai clienti. Si provvede quindi alla rimozione delle componenti pericolose e critiche (come le batterie e i condensatori), quindi alla macinazione della plastica, infine alla separazione delle componenti ferrose dalle altre. Lo si fa con un sistema di flottazione e il passaggio in due differenti vasche e a differenti densità. Prima per separare la frazione di metalli e plastiche pesanti che “affonda” (con ritardanti di fiamma e bromurati) da quella che galleggia, poi per separare la frazione metallica dalla plastica pesante.
Su ogni singola frazione sono condotte ulteriori ricerche volte all’analisi dei materiali ottenuti per migliorare i processi. Ne spiega i dettagli tecnici Fabio Bignotti, professore associato di Scienza e Tecnologia dei materiali: “In una prima fase studiamo i polimeri che compongono la frazione di plastica dopo il processo di macinazione, quindi analizziamo il processo di flottazione che pur su campioni di diversi stabilimenti offre, e questo è positivo, una ripartizione tra plastica leggera, pesante e resa metallica abbastanza costante”.
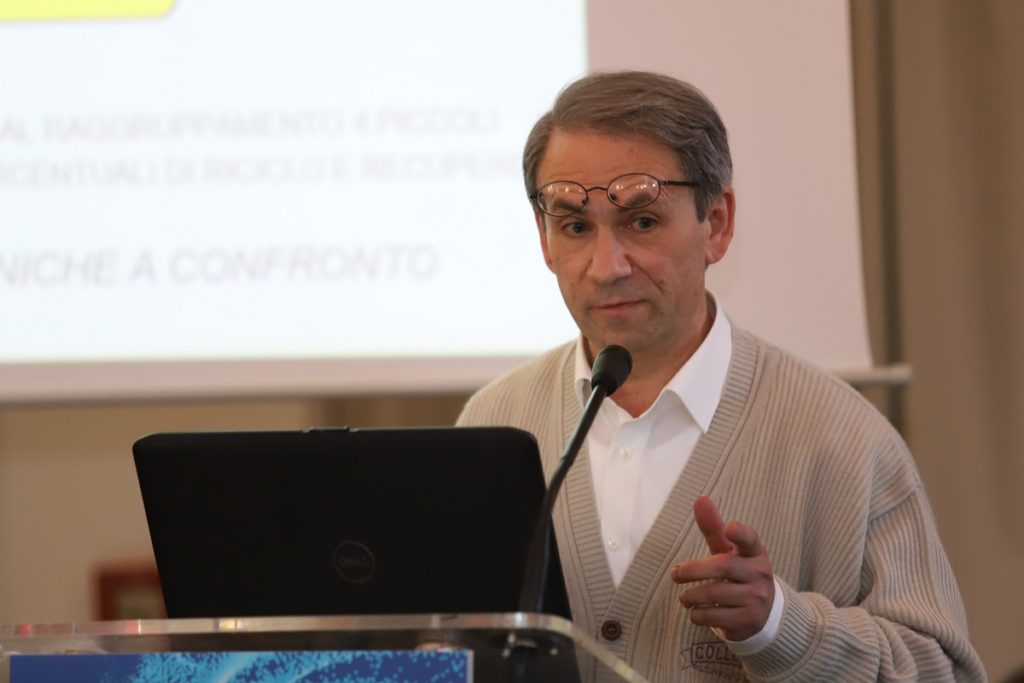
Variando alcuni parametri fisico/chimici delle vasche di flottazione (tra cui la densità) si migliora questo processo e poi si procede con un’ulteriore caratterizzazione delle frazioni di uscita conducendo ulteriori ricerche. Prosegue Bignotti: “Per esempio con un successivo processamento in estrusione effettuato in un impianto svedese che permette l’incremento delle quantità di recupero. L’introduzione di un processo di selezione ottico/digitale per la plastica pesante si rivela interessante su materiali plastici come PC e PC-ABS ma non su altri polimeri”.
I risultati
Il progetto dimostra come sia possibile migliorare i processi di trattamento di e selezione delle plastiche contenute nei rifiuti elettronici sia sotto il profilo quantitativo che qualitativo (-10% di scarti nelle frazioni, rispetto ai precedenti metodi), con un incremento rispetto ai dati della raccolta nazionale del 2019 di oltre 300 tonnellate (per oltre 17.200 tonnellate di raccolta complessiva).
Si tratta di plastiche che, opportunamente lavorate, possono essere impiegate per la costruzione di apparecchiature elettriche e di automobili, ma anche nell’oggettistica. A questi numeri si affianca la diminuzione della plastica pesante che verrà destinata necessariamente alla distruzione tramite inceneritore.
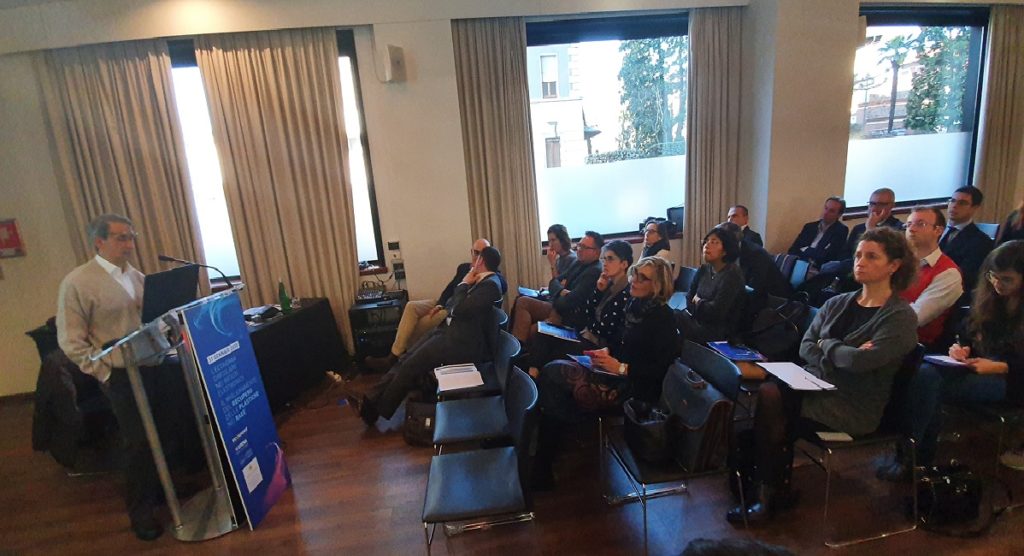
Per quanto riguarda la qualità dei materiali ottenuti è significativo il calo degli scarti nelle frazioni avviate al recupero (quindi plastica leggera e metalli), per una migliore collocabilità del materiale sul mercato. Il caso rivela come il coordinamento delle competenze delle nostre università, eccellenti, con l’impresa e le realtà del territorio, rappresenti un modello operativo efficace anche su temi e criticità che (con Raee) ci vedono tra i Paesi più avanti in Europa, pur in un contesto difficile e con non poche contraddizioni e lacune per quanto riguarda i regolamenti.
© RIPRODUZIONE RISERVATA