Tra le tecnologie più promettenti, solo in parte considerabili ancora come “emergenti”, perché hanno già offerto ampia prova della sua efficacia sul campo, i digital twin sono valutati, anche dagli analisti, sempre più fondamentali nei processi di innovazione in ottica Industria 4.0.
La possibilità di sfruttare un modello “vivo” per quanto digitale, di una linea di produzione, e quindi costruire una copia virtuale – per esempio di una macchina o di un impianto – in grado di replicare in tutto e per tutto il funzionamento reale (o di verificarne tutte le possibili alternative) rappresenta un’importante possibilità per lo sviluppo delle aziende che possono analizzare, verificare, ottimizzare e fare previsioni su prestazioni, ed efficienze di macchinari e prodotti, con un notevole risparmio sui costi. Ne parliamo con Alessandro Piglia, managing partner di Kairos3D.
Cosa fa Kairos3d e qual è l’idea alla base della sua costituzione? Come si inserisce la sua offerta nell’ambito di Industria 4.0?
Kairos3D è un’azienda innovativa torinese che produce Gilgamesh, piattaforma software 3D all’avanguardia per la creazione di digital twin 3D per il mondo industriale. L’azienda nasce nel 2010 con l’obiettivo di partecipare al profondo cambiamento nel dominio delle interfacce uomo-macchina, dove lo spazio bi-dimensionale per l’interazione ed il controllo viene rimpiazzato dallo spazio tridimensionale e dalla visione stereoscopica. Grazie alla nostra pregressa esperienza verticale nel campo dell’industria grafica, in Kairos3D abbiamo realizzato una piattaforma per il 3D interattivo specificamente finalizzata ai digital twin industriali. Siamo ora in una fase di estrema maturità del software, più specificamente alla sua release 4.0, che ci piace accostare (non a caso) al concetto di Industria 4.0.
Quali sono i principali ambiti di offerta con cui vi proponete sul mercato? Quali i punti distintivi?
Gilgamesh è una moderna piattaforma software che consente la trasformazione di modelli Cad 3D nei corrispondenti digital twin intelligenti: gemelli digitali di asset fisici, per supportarne le varie fasi del ciclo di vita. I digital twin 3D sono infatti potenti strumenti a supporto delle fasi di design, construction e operation di asset industriali come interi impianti, linee di produzione o specifici macchinari.
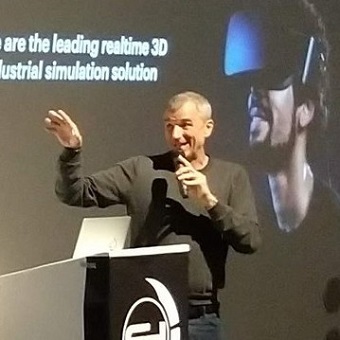
Grazie al focus esclusivo in campo industriale, abbiamo reso disponibili una serie di caratteristiche e funzionalità che il mercato ha ben recepito e riconosciuto come di grande valore, su tutte la capacità di sviluppare e rilasciare digital twin 3D intelligenti in tempi dell’ordine di settimane.
Questo è il nostro fattore distintivo principale: la possibilità di realizzare applicazioni 3D per l’Industria 4.0 con un altissimo rapporto qualità-prezzo. Questa caratteristica, unitamente alla strategia di prodotto aperta al coinvolgimento di partner, ci ha consentito di stringere alleanze con importanti player industriali come Emerson e Yokogawa, che integrano la nostra tecnologia nella loro offerta digitale, consentendoci di partecipare a progetti e gare in tutto il mondo.
Puoi raccontare alcuni ambiti concreti di applicazione?
I digital twin sono utilizzati da tempo nel mondo dell’aviazione: tutti sappiamo che cos’è un simulatore di volo. Bene, da più di un decennio quello stesso paradigma è stato adottato in altri settori di mercato, in particolare dall’industria energy/oil&gas, dove la formazione del personale necessita di una importante fase di training on the job. In questi settori, la disponibilità di digital twin degli impianti – tramite cui praticare in maniera sicura le procedure di conduzione ed esercitarsi nella gestione delle emergenze – rappresenta un grosso valore, sia per la formazione sia per gli aspetti di sicurezza (Hse).
Non è solo il comparto energy a beneficiare dei digital twin 3D; le funzionalità dei gemelli digitali trovano applicazione in molti altri settori, dall’edilizia all’industria pesante, dal manufacturing ai trasporti. Pensiamo ad esempio a chi costruisce linee di produzione o macchinari complessi: poter fornire assieme all’asset fisico il corrispondente gemello digitale (che include la manualistica e la possibilità di simulare procedure di manutenzione e best practice di conduzione), rappresenta un significativo valore aggiunto.
Oltre agli aspetti funzionali legati al training ed alla sicurezza industriale, i digital twin 3D forniscono altri valori di business. Ad esempio, stiamo osservando una crescita della domanda di mercato per gemelli digitali orientati alla visualizzazione dati ed all’asset health tracking: la possibilità di visualizzare lo stato di salute di un impianto attraverso l’interconnessione del suo gemello digitale 3D con i suoi sistemi di campo. I dati provenienti dai sistemi vengono “spalmati” in tempo reale sulla rappresentazione 3D, consentendo una visione geograficamente “contestualizzata” dei fenomeni (Kpi, allarmi, etc.) e facilitando il processo decisionale degli asset manager.
Non perdere tutti gli approfondimenti dello Speciale Industria 4.0
© RIPRODUZIONE RISERVATA